Проблемы в офсетной печати и методы их устранения
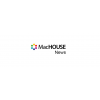
Проблема: Белый налет на офсетном полотне и форме.
Решение: Проверить жесткость воды при помощи лакмусовой бумаги. Если вода имеет жёсткость выше 14° (немецких), необходимо использовать буферные добавки в увлажнение для жёсткой воды. У фирмы Varn они имеют индекс 250.
Проблема: Выщипывание. Отрыв волокон или частиц поверхности бумаги в процессе печатания.
Причина: Низкая прочность поверхностного слоя бумаги.
Решение: Попробовать печатать на оборотной стороне или заменить бумагу. Если это невозможно, то положение может спасти предварительная запечатка бумаги бесцветным лаком.
Причина: Повышенна липкость краски:
Решение: Снизить липкость печатной краски, добавив AR—04 Compound, AL—Compound (Dong Yang Ink) или DruckOil (HuberGroup).
Причина: Повышенная липкость офсетной резины:
Решение: Разбрызгать на поверхность офсетной резины средство EASY START, INK-READI или заменить на менее липкое офсетное полотно.
Причина: Очень большое давление между офсетным и печатным цилиндром:
Решение: Проверить зазоры между цилиндрами, возвышение формы и декеля над контрольными кольцами. Установить минимальное давление. Ширина полосы контакта не должна быть больше 5-6 мм.
Проблема: Двоение печатных элементов. Появление несовпадающих изображений на офсетном полотне, одно яркое, другое блеклое.
Причина: Слабо натянуто офсетное полотно:
Решение: Сменить офсетные полотна. Можно снять старое офсетное полотно, дать ему отлежаться 2-3 часа и снова установить его с правильным натяжением. Используйте динамометрический ключ!
Причина: Очень большое давление между офсетным и печатным цилиндром:
Решение: Проверить зазоры между цилиндрами, возвышение формы и декеля над контрольными кольцами. Установить минимальное давление. Ширина полосы контакта не должна быть больше 5-6 мм.
Причина: Избыточная подача краски:
Решение: Заменить краску на ту, которая имеет больший кроющий эффект, например из серии InkRedible фирмы HuberGroup или Comax фирмы Dong Yang Ink.
Проблема: Загибание краев бумаги. Печатный лист теряет плоскостность.
Причина: Плохой микроклимат в помещении:
Решение: Контролируйте влажность в помещении типографии в пределах 48-58 при температуре 19-23 С. Можно попытаться прогнать бумагу через печатную машину без краски с одним увлажнением.
Проблема: Зажиривание (тенение) формы. Появление вуали, красочных пятен или полос на печатных оттисках в процессе печатания.
Причина: Дефекты печатной формы
Решение: Попытаться очистить ее поверхность средствами QUICK BLUE, PLATE PLUS, COMPLETE, CTP PLATE CLEANER (Varn). Если это не помогло - заменить печатную форму.
Причина: Загрязнены краской валики увлажняющей системы.
Решение: Загрязненные резиновые увлажняющие валики тщательно промыть METERING ROLLER CLEANER (MRC), Revitol (Varn). Затем смыть эти растворы увлажняющим раствором.
Причина: Малая подача увлажняющего раствора на печатную форму
Решение: Увеличить подачу раствора или содержание в ней изопропилового спирта.
Причина: Низкая кислотность увлажняющего раствора. Для обнаружения этой проблемы рекомендуется использовать pH-метр.
Решение: Проверить кислотность увлажняющего раствора, рН должен быть в пределах 5,2-5.5 (для листа).
Причина: Избыточная подача краски в красочную систему и на печатную форму
Решение: Отключить на некоторое время подачу краски, чтобы лишняя краска сошла с валиков. Для ускорения процедуры можно рекомендовать кратковременное включение смывочного ракеля или съем лишней краски с валиков с помощью листов мелованной бумаги.
Причина: Краска очень жидкая или разжижается нагревом в раскатной системе
Решение: Добавить в краску средство для повышения вязкости .
Причина: При корректировании в краску добавлено избыточное количество сиккатива. Количество сиккатива – Grafo Drier Extra в краске не должно превышать 2-5% от массы краски, сиккатива CO-06 DRIER - до 1%.
Причина: Повышенная кислотность бумаги:
Решение: Проверьте кислотность бумаги у поставщика. РН должен быть не ниже 5. В противном случае заменить бумагу.
Если имеет место неравномерное зажиривание по ширине изображения, это наиболее сложная ситуация. Когда вуаль появляется только в середине изображения или только по ее краям. В этом случае вышеперечисленные меры могут оказаться недостаточными, т.к. улучшение качества печати в одной области неизбежно ведет к ухудшению в другой.
Решение: Проверьте регулировки взаимного давления валиков красочного и увлажняющего аппарата. Проверьте геометрические отклонения и состояние поверхности валиков. В случае обнаружения дефектов - замените эти валики. В некоторых случаях подобную ситуацию могут выправить специальные добавки в увлажнение.
Проблема: Замедленное высыхание краски на оттисках.
Причина: Высокая кислотность увлажняющего раствора.
Решение: Добавить в краску до 3% сиккатива Grafo Drier Extra. Регулярно проверять кислотность увлажняющего раствора в процессе печатания тиража электронным РН-метром. Добавить до 15% изопропилового спирта.
Причина: Обильное увлажнение печатной формы.
Решение: Снизить подачу увлажняющего раствора. Чтобы не началось зажиривание формы, можно увеличить концентрацию изопропилового спирта.
Причина: При небольшой доле печатных элементов, печатная краска воспринимает много воды.
Решение: Чтобы увеличить подачу свежей краски, печатайте жирные линейки или плашки в хвосте изображения, которые затем обрежутся.
Причина: Эмульгирование краски с водой в процессе печатания.
Решение: Определить причину эмульгирования и устранить (см. п. “Эмульгирование”)
Причина: При корректировании печатных свойств краски введено большое количество вспомогательных веществ (разбавителей, паст и т.д.)
Решение: Печатать неразбавленными красками. Вводить не больше рекомендуемого количества вспомогательных средств. Общее количество добавок не должно превышать 5% от объема краски.
Причина: Толстый слой краски на оттиске.
Решение: Уменьшить подачу краски. Печатать более интенсивными красками, например Comax.
Причина: Бумага имеет повышенную кислотность.
Решение: Проверьте кислотность бумаги у поставщика. РН должен быть не ниже 5. Заменить бумагу.
Причина: Низкая температура или повышенная влажность воздуха в помещении.
Решение: Нормальный уровень температуры в цехе должен быть 19-23° С в теплое время года, относительная влажность 50-60%; в холодное время 18°-22°С и 45-55%
Причина: Недостаточная акклиматизация краски и бумаги.
Решение: Акклиматизация материалов в цехе не менее 24 часов.
Проблема: Засыхание краски на машине.
- По краям валов при не полностью используемoм формате:
Решение: Периодически смывать красочный аппарат. Поставить в кипсейку ограничивающие клинья.
- При неработающей машине или во время приладки:
Решение: Перед простоем машины нанести на красочные валики средства INK-READI.
Проблема: Меление. Осыпание краски или “сползание” красочного слоя с высохшего оттиска под действием легкого трения.
Решение: Замените краску на специализированную с повышенной стойкостью к истиранию – например Resista или Comax.
Причина: Обильная подача увлажняющего раствора на печатную форму.
Решение: Печатать с минимальной подачей увлажняющего раствора на форму.
Причина: Повышенная кислотность увлажняющего раствора.
Решение: Регулярно проверять кислотность увлажняющего раствора в процессе печатания тиража электронным РН-метром.
Причина: Бумага с пониженной впитывающей способностью.
Решение: Если нет возможности заменить бумагу, то печатать неразбавленными красками или печатать краска + защитный лак.
Причина: Краска сильно разбавлена различными растворителями.
Решение: Печатать неразбавленными красками. Вводить не больше рекомендуемого количества вспомогательных средств. Общее количество добавок не должно превышать 5% от объема краски.
Если “меление” своевременно не замечено, то во избежание брака запечатать оттиски тонким слоем прозрачных белил или прозрачным глянцевым или матовым лаком.
Проблема: Наслоение краски на офсетное полотно.
Причина: В красочную систему подается большое количество краски.
Решение: Снизить подачу краски или печатать высокоинтенсивными красками, такими как Comax.
Причина: Повышенная липкость краски.
Решение: Снизить липкость печатной краски, добавив AL—Compound, AR—04 Compound или Paste Reducer 10 T 9998
Причина: Попадание бумажной пыли в краску.
Решение: Чаще делать остановки в процессе печати и протирать офсетное полотно.
Причина: Печатание ведется холодными красками.
Решение: Акклиматизировать краску в помещении печатного цеха не менее 24 часов.
Причина: Обильная подача увлажняющего раствора на печатную форму.
Решение: Печатать с минимальной подачей увлажняющего раствора на форму.
Причина: Слабое натяжение офсетного полотна.
Решение: Проверить натяжение офсетного полотна, особенно в местах наслоения краски.
Проблема: Низкая прочность оттиска к истиранию. Закрепившаяся на оттиске краска стирается при дальнейших отделочных операциях.
Причина: Несоответствие печатной краски бумаге.
Решение: Печатать красками с повышенной прочностью к истиранию Resista, Impression (Huber) или Comax (Dong Yang Ink).
Причина: Избыточное применение противоотмарочного порошка.
Решение: Избегать чрезмерного применения противоотмарочных средств. Не применять стандартные порошки на минеральной основе, а использовать Spray Powder (Varn) соответствующего диаметра.
Причина: Высокая кислотность бумаги и в результате замедление реакции окислительной полимеризации при закреплении краски
Решение: Проверьте кислотность бумаги у поставщика. РН должен быть не ниже 5. Заменить бумагу.
Причина: Недостаточное закрепление.
Решение: Перед печатью добавить в краску до 3% сиккатива GrafoDrierExtra или до 1% CO-06 DRIER. После печати лакировать защитным лаком. На плохо впитывающих материалах печатать красками серии Foil.
Причина: При корректировании печатных свойств краски введено большое количество вспомогательных веществ (разбавителей, паст и т.д.)
Решение: Печатать неразбавленными красками. Вводить не больше рекомендуемого количества вспомогательных веществ. Общее количество добавок не должно превышать 5% от объема краски.
Причина: Повышенная кислотность увлажняющего раствора.
Решение: Регулярно проверять кислотность увлажняющего раствора в процессе печатания тиража.
Проблема: Неточности приводки. Нелинейные несовмещения изображений разных цветов между отдельными прогонами бумаги, либо между секциями печатной машины.
Причина: Не отрегулированы давления между офсетными и печатными цилиндрами на разных секциях.
Решение: Установите необходимые зазоры между цилиндрами ручками натиска строго в соответствии с инструкцией пользователя печатной машины.
Установите минимальный натиск на бумагу.
Снимите офсетные полотна и измерьте суммарную толщину декеля с поддекельным полотном. Расхождения в толщине между секциями и по площади должны быть не более 0.03 мм. Смените декель или подкладку.
Причина: Большая подача увлажнения.
Решение: Снизьте подачу увлажнения и краски до минимума. Если при этом начинается зажиривание формы, добавьте большее кол-во изопропилового спирта в увлажняющий раствор.
Причина: Деформация бумаги из-за недостаточной механической прочности.
Решение: Смените ориентацию бумаги на 90 градусов. Смените бумагу.
Проблема: Оголение валиков. При этом ухудшается равномерный перенос краски на печатную форму, снижается качество оттисков.
Причина: Эмульгирование краски.
Решение: См. п. “Эмульгирование краски”.
Причина: Высокая кислотность увлажняющего раствора.
Решение: Регулярно проверять кислотность увлажняющего раствора в процессе печатания тиража.
Причина: Краска “короткая”.
Решение: Откорректировать краску, добавив стабилизатор краски или печатное масло.
Причина: Глянец на валиках.
Решение: Очистить валики средством S.R.R., Jelly Revitol, Calcium Degleser (Varn).
Проблема: Oтмарывание. Переход краски с запечатанной стороны листа на оборотную сторону следующего оттиска.
Причина: Мелованная бумага повышенной гладкости или литого мелования.
Решение: Использовать краски, предназначенные для печати на мелованных бумагах. Такие как серия красок Aronon-T или CoMax.
Причина: Излишняя насыщенность краски на оттиске, особенно при печати плашек.
Решение: Плашки, по возможности, не растрировать, а печатать чистыми цветами, например, по PANTONE.
Причина: Замедленное первоначальное закрепление краски (“схватывание”) на оттиске.
Решение: Добавить в краску сикатив CO-06 DRIER.
Используйте противоотмарочные порошки различной степени зернистости.
Причина: Эмульгирование краски в результате излишней подачи увлажняющего раствора.
Решение: См. п. “Эмульгирование”.
Проблема: Плохое вращение краски в красочном ящике. Контакт краски с дукторным цилиндром наблюдается в виде полошения; в результате прерывается подача краски от дуктора через передаточный валик в красочную систему. Оттиски получаются мало интенсивными.
Причина: Kраска тиксотропна.
Решение: Перед запуском машины краску тщательно перемешать в красочном ящике с добавлением печатного масла. Это сделает краску более эластичной.
Причина: Пониженная липкость краски.
Решение: Повысить липкость краски добавив олифу .
Причина: Низкая температура краски.
Решение: Акклиматизировать краску в помещении печатного цеха не менее 24 часов.
Проблема: Плохое наложение красок при печатании “по-сырому”.
Причина: Большая толщина красочного слоя при печатании первой краской.
Решение: Снизить подачу краски, печать вести, соблюдая денситометрические нормы.
Причина: Нарушено правило липкости краски при печатании на многокрасочных машинах.
Решение: При печатании на многокрасочных машинах необходимо, чтобы липкость каждой последующей краски была меньше предыдущей. Снизить липкость печатной краски с помощью печатного масла или средства AL—Compound.
Причина: Стекленение красок.
Решение: См.п. “Стекленение красок”.
Проблема: Полошение. Образование поперечных полос на оттисках с крупными сплошными или растровыми печатными элементами.
Причина: Изношены валики или подшипники печатной машины.
Решение: Проверьте полосы контакта между валиками красочного и увлажняющего аппарата.
Если шаг полос равняется шагу шестерен привода, то причина в износе зубчатых передач или увеличенному давлению между шестернями.
Вызовите специалиста.
Причина: Неверно натянуто офсетное полотно.
Решение: Переустановить.
Проблема: Проблемы с подачей бумаги в печатную машину. Частые остановки печатания из-за двойных листов или неподачи бумаги со стола самонаклада.
Причина: Сильно электризованная бумага.
Решение: Проверить состояние устройства снятия статического заряда, при необходимости металлическими щетками (при выключенной машине) очистить разрядники от образовавшего нагара.
Использовать антистатические аэрозоли для снятия заряда с приемной и подающей стопы.
Причина: Не настроены механизмов подачи и разделения листов и пневматики на самонакладе машины.
Решение: Проверьте по инструкции настройки вакуума, раздува, положение стопы по высоте, размещение листоотделительных пружинок в двух плоскостях и т.п.
Причина: Слишком сухой воздух в помещении. Поставьте кондиционер с автоматическим поддержанием микроклимата (с регулировкой влажности). Можно использовать увлажнители, чтобы довести относительную влажность в помещении до 40-60%.
Причина: Плохо уложена стопа на самонакладе.
Решение: Перетряхните стопу и уложите ее снова. Загружайте бумагу мелкими порциями.
Проблема: Пятнистость. Неравномерное распределение краски на фоновых оттисках. При многокрасочной печати последующие краски наносятся на предыдущие с неравномерным блеском.
Причина: Появление на оттисках структуры ткани чехлов увлажняющих валиков.
Решение: Проверьте натяжение чехлов. Отрегулируйте давление увлажняющих валиков с помощью бумажных щупов. Между накатными валиками и формой полоски 80 гр. бумаги должны проходить с усилием, но без разрыва. На остальных валиках давление должно быть чуть меньше.
Заменить чехлы.
Причина: Плохое вращение краски в красочном ящике. Пятнистость выражается чередованием светлых и темных полос на оттиске по направлению вращения печатного цилиндра.
Решение: См.п. “Плохое вращение краски в красочном ящике”.
Причина: Пониженная липкость краски. Она плохо раскатывается в красочной системе и плохо наносится накатными валиками на печатную форму.
Решение: Откорректировать краску введением олифы .
Причина: Очень вязкая краска.
Решение: Использовать для снижения вязкости краски печатное масло или средства AR—04 Compound.
Причина: Неоднородная бумага.
Решение: Заменить бумагу.
Причина: Обильное увлажнение печатной формы, особенно на предыдущих секциях.
Решение: Отрегулировать подачу увлажняющего раствора. Печатать с минимальным увлажнением.
Проблема: Растискивание штрихов и растровых точек на оттиске.
Причина: Избыточная подача краски в красочную систему и на печатную форму.
Решение: С помощью макулатурных листов бумаги снять излишки краски с валов, уменьшить подачу краски.
Причина: При корректировке в краску введено большое количество разбавителей.
&
Последние статьи
Все публикации10 увлекательных фактов о Pantone: тайны мирового авторитета цветов
Компания Pantone стала синонимом цветового совершенства и культурного влияния с момента своего основания в 1963 году. За...
Mark Andy открывает новый "Инновационный хаб" в Варшаве: Революционные возможности для украинских предприятий
В июне 2025 года произошло историческое событие для полиграфической индустрии региона - Mark Andy торжественно открыла р...
MacHOUSE на Plast Expo UA 2025: Інноваційні рішення для друку та виробництва пластикових виробів
MacHOUSE на Plast Expo UA 2025 MacHOUSE на Plast Expo UA 2025 Інно...
Искусственный интеллект в полиграфии: Новая эра креативности и эффективности
В мире, где технологические инновации приходят из Кремниевой долины, мало кто ожидал, что полиграфия — отрасль с м...
Насыщенный, теплый коричневый - Pantone представил цвет года 2025
Улавливая глобальное настроение связи, комфорта и гармонии Программа «Цвет года по версии Pantone» привле...